Plans, directs, and coordinates activities concerned with design, construction, modification, and maintenance of equipment and machinery in industrial plant: Establishes standards and policies for environmental control, installation, modification, quality control, testing, operating procedure, inspection, and maintenance of equipment, according to engineering principles and safety regulations. Will support plant projects and equipment upgrades. Maintain a high level of detail, safety awareness in a fast-paced food plant environment. Essential Duties and Responsibilities include the following. Other duties may be assigned. Directs maintenance of plant buildings and coordinates requirements for new designs, surveys, and maintenance schedules for equipment and machinery. Prepares bid sheets and contracts for construction and facilities acquisition. Owns the plant capital budget and monitors expenditure of funds in budget. Utilizes Initiative Management tools to ensure the successful start-up of newly installed machines and equipment to ensure fulfillment of contract specifications. Coaches the organization to provide project proposal or plans to ensure the successful implementation of projects to include time frames, funding limitations, procedures for accomplishing project, staffing requirements, and allotment of available resources to various phases of project. Directs and coordinates activities of project personnel to ensure project progresses on schedule and within prescribed budget. Provides guidance to ensure the plant utilizes RSLogix and Allen Bradley Software to program and troubleshoot PLC driven systems. Assist the plant in repair all facility systems and equipment, i.e. processing, packaging warehouse, material receiving, HVAC units, air compressors and other facility systems when needed. Possess key skills in the following areas: electrical to include 3 phase, mechanical aptitude, fluid power skills, general machining skills, strong preventative maintenance skills. Attend and actively participate in various plant meetings and functions. Must have general interaction skills to work with various departments. Able to read and interpret written information and able to write clearly and informatively. Utilize manual and computer systems to research and order parts enter and update work orders and PMs, etc. Provide training to build the skill level of operations and maintenance team members. Assist in worker training in areas such as safety/environmental laws and regulations, hazardous condition monitoring and use of safety equipment as it relates to engineering. Assist in safety and environmental audits, facility inspections, machinery, and safety equipment to identify and correct potential hazards and to ensure regulatory compliance. Thorough knowledge of EPA, OSHA, HAZMAT, RCRA, DOT, PSM and/or other Federal and State regulations pertaining to safety, health and environmental various regulatory requirements pertaining to manufacturing facilities. Coordination of the plants environmental improvement and sustainability projects Directs and coordinates activities related to the operation and maintenance of the on-site Water Treatment Systems and Anhydrous Ammonia at some locations. Establishes protocols and monitoring to ensure environmental compliance and reporting for facility. Supply and maintain ones own tools to meet the maintenance requirements. Enforces all food safety and food quality policies and procedures. Must perform additional duties assigned by manager or as required to support the needs of the business. May advice on structural safety requirements based on failure mode analysis of such factors as fatigue, stability, stress, concentration, and creep. Strives to continuously build knowledge and skills and shares expertise with others. Exhibits sound and accurate judgment and includes appropriate people in decision-making process. Follows instructions, responds to management direction Works with Maintenance Manager to prioritize and plan work activities and completes work in timely manner. Initiates purchase order for parts and machines. Works within approved budget and conserves organizational resources. Follows policies and procedures and observes safety and security procedures. Uses equipment and materials properly and reports potentially unsafe conditions. Is consistently at work and on time and commits to long hours of work when necessary to reach goals. Supervisory Responsibilities Supervises one (1) Mechanical Engineer and one (1) Electrical Engineer. Carries out supervisory responsibilities in accordance with the organization's policies and applicable laws. Responsibilities include interviewing, hiring, and training employees; planning, assigning, and directing work; appraising performance; rewarding and disciplining employees; addressing complaints and resolving problems. Qualifications: To perform this job successfully, an individual must be able to perform each essential duty satisfactorily. The requirements listed below are representative of the knowledge, skill, and/or ability required. Reasonable accommodations may be made to enable individuals with disabilities to perform the essential functions. Education and/or Experience Bachelor's degree (B. A.) from four-year college or university in a related engineering field preferred, with a minimum of five years related experience in a management position.; or equivalent combination of education and experience. Technical Skills To be successful as a Plant Engineer you must possess the basic skills needed to troubleshoot many types of equipment. Example of these skills are: Mechanical: Understand, utilize, trouble-shoot and maintain different types and applications of pumps, piping, fittings, reducers, bearings, lubricants, sprockets, chains, locking collars, shafts, drums, belting, hydraulics, pneumatics, conveyors, cams, hand tools, gauges, etc. Electrical: Understand, utilize, trouble-shoot and maintain different systems and equipment powered by industrial electricity; including AC and DC power, single phase and three phase power, wiring, motors, continuity, resistance, motor starters, power supplies, disconnects, fuses, breakers, overload heaters, variable frequency drives, drives, air logic, relay logic, field devices, etc. Electronics/Controls: Understand, utilize, trouble-shoot, calibrate and maintain different systems used for industrial controls: relay logic, field instrumentation, PLC hardware and ladder logic, other computer systems and processors, resistance, reactance, capacitance, hand meters, meg-o-meter, solenoids, control valves, field controllers etc. Equipment Experience: Must have experience on specific equipment. This equipment includes boilers, air compressors, motors, gearboxes, conveyor systems, pumps and other common components found in a manufacturing environment. Mathematical Skills Ability to work with mathematical concepts such as probability and statistical inference, and fundamentals of plane and solid geometry and trigonometry. Ability to apply concepts such as fractions, percentages, ratios, and proportions to practical situations. Reasoning Ability Ability to solve practical problems and deal with a variety of concrete variables in situations where only limited standardization exists. Ability to interpret a variety of instructions furnished in written, oral, diagram, or schedule form. Computer Skills To perform this job successfully, an individual should have knowledge of Internet software; Inventory software; Project Management software; Spreadsheet software and Word Processing software Physical Demands The physical demands described here are representative of those that must be met by an employee to successfully perform the essential functions of this job. Reasonable accommodations may be made to enable individuals with disabilities to perform the essential functions. While performing the duties of this Job, the employee is regularly required to stand; use hands to finger, handle, or feel; push, pull, and reach with hands and arms and talk or hear. The employee is frequently required to walk; climb or balance; stoop, kneel, crouch, or crawl and taste or smell. The employee is occasionally required to sit. The employee must frequently lift and/or move up to 50 pounds. Specific vision abilities required by this job include close vision, distance vision, color vision, peripheral vision, depth perception and ability to adjust focus. Work Environment The work environment characteristics described here are representative of those an employee encounters while performing the essential functions of this job. Reasonable accommodations may be made to enable individuals with disabilities to perform the essential functions. While performing the duties of this Job, the employee is regularly exposed to moving mechanical parts; fumes or airborne particles and toxic or caustic chemicals. The employee is frequently exposed to wet and/or humid conditions and risk of electrical shock. The employee is occasionally exposed to high, precarious places; outside weather conditions; extreme cold; extreme heat and vibration. The noise level in the work environment is usually loud and requires that hearing protection be worn in all production areas.
1st Shift
PI143516380
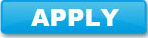
|